الفولاذ المقاوم للصدأ الأوستنيتي، كما يوحي اسمه، لديه هيكل الأوستينيت. المعالجة الحرارية للفولاذ المقاوم للصدأ الأوستنيتي مهم جدًا لأن المهمة المهمة للفولاذ المقاوم للصدأ الأوستنيتي هي مقاومة التآكل. إذا كانت المعالجة الحرارية غير مناسبة، فسوف تنخفض مقاومتها للتآكل بشكل كبير. هذه المقالة تخبرك بشكل رئيسي عن ذلك. المعالجة الحرارية للفولاذ المقاوم للصدأ الأوستنيتي.
الفولاذ المقاوم للصدأ الأوستنيتي هو الفولاذ المقاوم للصدأ الشائع (18-8 فولاذ). على سبيل المثال، العديد من أدوات المائدة في المطبخ مصنوعة من الفولاذ الأوستنيتي المقاوم للصدأ. الفولاذ المقاوم للصدأ الأوستنيتي، كما يوحي اسمه، لديه هيكل الأوستينيت. إنه غير مغناطيسي وليس له صلابة.
يتمتع الفولاذ المقاوم للصدأ الأوستنيتي بمقاومة قوية جدًا للتآكل في البيئات المؤكسدة. يمكن ببساطة فهم ما يسمى بالبيئة المؤكسدة على أنها بيئة تحتوي على المزيد من الأكسجين. يتمتع الفولاذ المقاوم للصدأ الأوستنيتي بصلابة جيدة وسهل المعالجة والتشكيل، لذلك فهو يتمتع بمجموعة واسعة من الاستخدامات.
يستخدم الفولاذ المقاوم للصدأ الأوستنيتي بشكل رئيسي لأغراض مقاومة التآكل، والمعالجة الحرارية لها تأثير كبير عليه. تعتمد مقاومة التآكل ومقاومة الأحماض للفولاذ المقاوم للصدأ الأوستنيتي بشكل أساسي على تخميل السطح. إذا لم يكن بالإمكان الحفاظ على تخميل السطح، فسوف يتآكل.
ولذلك، الفولاذ المقاوم للصدأ ليست مقاومة للصدأ تمامًا، فهي مناسبة فقط للبيئات المؤكسدة والبيئات الحمضية. ليس لديها مقاومة قوية للأيونات الخاصة. تؤثر المعالجة الحرارية للفولاذ المقاوم للصدأ الأوستنيتي بشكل رئيسي على قدرة التخميل للطبقة السطحية، وبالتالي تؤثر على أداء التآكل.
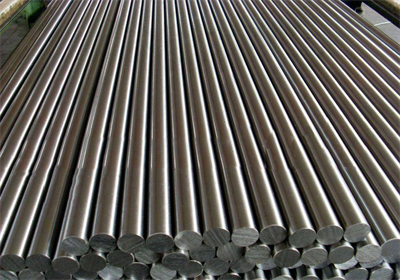
304 منحنى الاستقطاب الفولاذ المقاوم للصدأ، تظهر منطقة التخميل الأنود
التآكل الموحد هو ظاهرة التآكل الأكثر شيوعًا، ويعتمد التآكل الموحد على التوزيع الموحد لعناصر الكروم. تؤثر المعالجة الحرارية على توزيع عناصر الكروم، مما يؤثر بشكل طبيعي على مقاومة التآكل الموحدة للفولاذ المقاوم للصدأ الأوستنيتي.
يعد التآكل الحبيبي أيضًا أحد خصائص التآكل المهمة لتقييم الفولاذ المقاوم للصدأ الأوستنيتي. بشكل عام، إذا تم تحسس الفولاذ المقاوم للصدأ الأوستنيتي وترسب عدد كبير من الكربيدات الشبيهة بالخرز عند حدود الحبوب، فسيتم تقليل أداء التآكل بين الحبيبات بشكل كبير.
إذا تم تحسس الفولاذ المقاوم للصدأ الأوستنيتي، فسوف يحدث تآكل شديد بين الحبيبات حتى في بيئة كهروكيميائية عادية جدًا.
يعد تكسير التآكل الناتج عن الإجهاد هو أكثر حالات الفشل شيوعًا في الفولاذ المقاوم للصدأ الأوستنيتي. يجب على الجميع ملاحظة أن التشقق الناتج عن التآكل الإجهادي يعتمد على عاملين رئيسيين:
أولاً، يجب أن يكون هناك إجهاد، والذي قد يكون إجهاداً تطبيقياً أو إجهاداً متبقياً؛
ثانيًا، الأيونات الحساسة للتكسير بسبب التآكل الإجهادي، مثل أيونات الهالوجين، وخاصة أيونات الكلوريد، هي الأكثر شيوعًا.
عندما يتم استخدام الفولاذ المقاوم للصدأ الأوستنيتي، غالبًا لا يتم استخدام قدرته على تحمل الإجهاد، لذلك يجب إيلاء اهتمام خاص للإجهاد المتبقي لأنه في بيئة تحتوي على أيونات الكلوريد، سيؤدي الإجهاد المتبقي إلى تشقق التآكل الإجهادي. طريقة إزالة الإجهاد المتبقي هي التلدين لتخفيف الإجهاد.
التآكل الحفري هو الشكل الأكثر رعبا للتآكل. ويقال إنه التآكل الأكثر رعبا، ومن الأنسب استخدام مقولة من القدماء لوصف هذه المشكلة: "ينهار سد طوله ألف ميل في عش النمل".
هناك سببان رئيسيان لحدوث التآكل:
أولاً، إذا كان تكوين المواد غير متساوٍ، مثل التحسس، فإن الفولاذ المقاوم للصدأ الأوستنيتي يكون عرضة بشكل خاص للتآكل؛
ثانيًا، تركيز الوسائط المسببة للتآكل البيئي غير متساوٍ، وهو أيضًا سبب التآكل.
بمجرد حدوث التآكل، سيتم تدمير طبقة فيلم التخميل المحلية، وسيكون هناك منافسة بين الحالة النشطة وحالة التخميل. وبمجرد عدم إمكانية حدوث التخميل، سيستمر التآكل حتى يتم ثقب المكون.
لا يحتوي الفولاذ المقاوم للصدأ الأوستنيتي على نقطة تحول في الطور الصلب من درجة حرارة الغرفة إلى درجة حرارة عالية. الغرض الرئيسي من المعالجة الحرارية هو إذابة الكربيدات المتولدة أثناء المعالجة في المصفوفة، مما يجعل توزيع عناصر السبائك أكثر اتساقًا.
تسخين الفولاذ المقاوم للصدأ الأوستنيتي إلى درجة حرارة عالية لإذابة الكربيدات في المصفوفة، ثم تبريده بسرعة إلى درجة حرارة الغرفة. خلال هذه العملية، لن يتصلب الفولاذ المقاوم للصدأ الأوستنيتي لأنه لا يوجد تحول طوري وستبقى الحالة الأوستنيتي في درجة حرارة الغرفة. وتسمى هذه العملية معالجة المحاليل الصلبة.
في معالجة المحاليل الصلبة، يكون الغرض من التبريد السريع هو فقط جعل توزيع ذرات الكربون وعناصر صناعة السبائك أكثر اتساقًا.
أثناء معالجة المحلول الصلب للفولاذ المقاوم للصدأ الأوستنيتي، إذا كان معدل التبريد بطيئًا جدًا، مع انخفاض درجة الحرارة، تنخفض قابلية ذوبان ذرات الكربون في المصفوفة، وسوف تترسب الكربيدات. علاوة على ذلك، من السهل بشكل خاص دمج ذرات الكربون مع الكروم لتكوين كربيدات M23C6، والتي يتم توزيعها على حدود الحبوب. يحدث استنفاد الكروم في حدود الحبوب ويحدث التحسس.
بعد حدوث التحسس في الفولاذ المقاوم للصدأيجب تسخينه فوق 850 درجة مئوية. سوف تذوب الكربيدات في محلول صلب، ومن ثم يمكن للتبريد السريع أن يحل مشكلة التحسس.