オーステナイト系ステンレス鋼は、その名の通りオーステナイト組織を持っています。 オーステナイト系ステンレス鋼の熱処理 オーステナイト系ステンレス鋼の重要な役割は耐食性であるため、これは非常に重要です。 熱処理が適切でないと耐食性が著しく低下します。 この記事では主にそれについて説明します。 オーステナイト系ステンレス鋼の熱処理。
オーステナイト系ステンレス鋼は一般的なステンレス鋼(18-8鋼)です。 例えば、キッチンにある食器の多くはオーステナイト系ステンレス鋼で作られています。 オーステナイト系ステンレス鋼は、その名の通りオーステナイト組織を持っています。 非磁性であり、焼入性がありません。
オーステナイト系ステンレス鋼は、酸化環境において非常に強い耐食性を持っています。 いわゆる酸化環境とは、単純に酸素を多く含む環境として理解できます。 オーステナイト系ステンレス鋼は靭性に優れ、加工・成形が容易なため、幅広い用途に使用されています。
オーステナイト系ステンレス鋼は主に耐食性を目的として使用されており、熱処理が大きく影響します。 オーステナイト系ステンレス鋼の耐食性と耐酸性は主に表面不動態化に依存します。 表面の不動態化を維持できない場合、腐食が発生します。
したがって、 オーステナイト系ステンレス鋼 完全なステンレスではなく、酸化環境や酸性環境にのみ適しています。 特殊なイオンに対しては強い耐性はありません。 オーステナイト系ステンレス鋼の熱処理は主に表面層の不動態化能力に影響を与え、そのため腐食性能に影響を与えます。
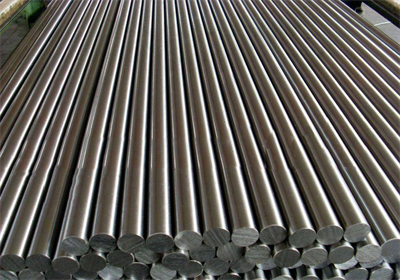
304 ステンレス鋼の分極曲線、アノード不動態化ゾーンが表示されます。
均一腐食は最も一般的な腐食現象であり、均一腐食はクロム元素の均一な分布に依存します。 熱処理はクロム元素の分布に影響を与え、当然、オーステナイト系ステンレス鋼の均一な耐食性にも影響を与えます。
粒界腐食もオーステナイト系ステンレス鋼を評価する上で重要な腐食特性の一つです。 一般に、オーステナイト系ステンレス鋼が鋭敏化して粒界にビーズ状炭化物が多数析出すると、粒界腐食性能が大幅に低下します。
オーステナイト系ステンレス鋼が鋭敏化すると、ごく一般的な電気化学的環境でも重大な粒界腐食が発生します。
応力腐食割れは、オーステナイト系ステンレス鋼の最も一般的な破損モードです。 応力腐食割れは次の XNUMX つの主な要因によって左右されることに誰もが注意する必要があります。
まず、応力が存在する必要があります。これには、適用応力または残留応力が考えられます。
第二に、ハロゲンイオン、特に塩化物イオンなどの応力腐食割れに敏感なイオンが最も一般的です。
オーステナイト系ステンレス鋼を使用する場合、応力耐性が生かされていない場合が多いため、塩素イオンを含む環境では残留応力により応力腐食割れが発生するため、残留応力には特に注意が必要です。 残留応力を除去する方法が歪取り焼鈍です。
孔食は腐食の中で最も恐ろしい形態です。 これは最も恐ろしい腐食であると言われており、この問題を説明するには、「千マイルの堤防がアリの巣で崩れる」という古代人の言葉が最も適切です。
孔食が発生する主な原因は次の XNUMX つです。
まず、材料組成が不均一である場合(鋭敏化など)、オーステナイト系ステンレス鋼は特に孔食を起こしやすくなります。
第二に、環境腐食性媒体の濃度は不均一であり、これも孔食の原因となります。
孔食が発生すると、局所的な不動態皮膜層が破壊され、活性状態と不動態状態が競合します。 不動態化が発生できなくなると、部品に穴が開くまで孔食が続きます。
オーステナイト系ステンレス鋼は室温から高温まで固相変態点を持ちません。 熱処理の主な目的は、加工中に生成した炭化物をマトリックスに溶解し、それによって合金元素の分布をより均一にすることです。
オーステナイト系ステンレス鋼を高温に加熱して炭化物をマトリックスに溶解させた後、室温まで急冷します。 このプロセス中、相変態が起こらず、オーステナイト状態が室温で維持されるため、オーステナイト系ステンレス鋼は硬化しません。 この処理を固溶体処理といいます。
固溶体処理における急速冷却の目的は、炭素原子と合金元素の分布をより均一にすることだけです。
オーステナイト系ステンレス鋼の固溶化処理において、冷却速度が遅すぎると、温度が低下するにつれて基地中の炭素原子の溶解度が低下し、炭化物が析出してしまいます。 さらに、炭素原子は特にクロムと結合して M23C6 炭化物を形成しやすく、粒界に分布します。 粒界でクロムの枯渇が起こり、鋭敏化が起こります。
感作が起こった後、 オーステナイト系ステンレス鋼、850℃以上に加熱する必要があります。 炭化物は固溶体に溶解し、その後急速に冷却することで鋭敏化の問題を解決できます。