Austenitisch roestvast staal heeft, zoals de naam al aangeeft, een austenietstructuur. De warmtebehandeling van austenitisch roestvrij staal is erg belangrijk omdat de belangrijke taak van austenitisch roestvast staal corrosiebestendigheid is. Als de warmtebehandeling onjuist is, zal de corrosieweerstand aanzienlijk worden verminderd. Dit artikel vertelt je er vooral over. Warmtebehandeling van austenitisch roestvast staal.
Austenitisch roestvast staal is een veelgebruikt roestvast staal (18-8 staal). Veel serviesgoed in de keuken is bijvoorbeeld gemaakt van austenitisch roestvrij staal. Austenitisch roestvast staal heeft, zoals de naam al aangeeft, een austenietstructuur. Het is niet-magnetisch en heeft geen hardbaarheid.
Austenitisch roestvrij staal heeft een zeer sterke corrosieweerstand in oxiderende omgevingen. De zogenaamde oxiderende omgeving kan eenvoudigweg worden opgevat als een omgeving die meer zuurstof bevat. Austenitisch roestvast staal heeft een goede taaiheid en is gemakkelijk te verwerken en te vormen, waardoor het breed inzetbaar is.
Austenitisch roestvast staal wordt voornamelijk gebruikt voor corrosiebestendigheid, en warmtebehandeling heeft hierop een grote invloed. De corrosiebestendigheid en zuurbestendigheid van austenitisch roestvast staal zijn voornamelijk afhankelijk van de passivatie van het oppervlak. Als de passivatie van het oppervlak niet kan worden gehandhaafd, zal het corroderen.
daarom Austenitisch roestvrij staal is niet volledig roestvrij, het is alleen geschikt voor oxiderende omgevingen en zure omgevingen. Het heeft geen sterke weerstand tegen speciale ionen. De warmtebehandeling van austenitisch roestvast staal beïnvloedt voornamelijk het passivatievermogen van de oppervlaktelaag, waardoor de corrosieprestaties worden beïnvloed.
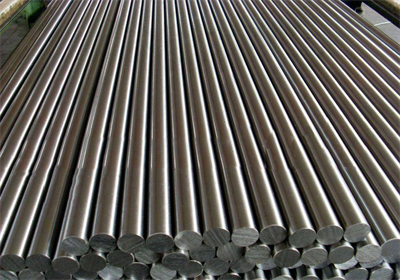
304 roestvrijstalen polarisatiecurve, anode-passiveringszone verschijnt
Uniforme corrosie is het meest voorkomende corrosieverschijnsel en uniforme corrosie hangt af van de uniforme verdeling van chroomelementen. Warmtebehandeling beïnvloedt de verdeling van chroomelementen, wat op natuurlijke wijze de uniforme corrosieweerstand van austenitisch roestvrij staal beïnvloedt.
Intergranulaire corrosie is ook een van de belangrijke corrosie-eigenschappen voor het evalueren van austenitisch roestvast staal. Over het algemeen geldt dat als austenitisch roestvast staal gevoelig wordt gemaakt en een groot aantal kraalachtige carbiden neerslaat op de korrelgrenzen, de intergranulaire corrosieprestaties ervan aanzienlijk worden verminderd.
Als austenitisch roestvast staal gevoelig wordt gemaakt, zal er zelfs in een heel gewone elektrochemische omgeving ernstige intergranulaire corrosie optreden.
Spanningscorrosiescheuren zijn de meest voorkomende faalwijze van austenitisch roestvast staal. Iedereen moet er rekening mee houden dat spanningscorrosiescheuren afhankelijk zijn van twee belangrijke factoren:
Ten eerste moet er sprake zijn van spanning, dit kan toegepaste spanning of restspanning zijn;
Ten tweede zijn ionen die gevoelig zijn voor spanningscorrosie, zoals halogeenionen, vooral chloride-ionen, de meest voorkomende.
Wanneer austenitisch roestvrij staal wordt gebruikt, wordt vaak geen gebruik gemaakt van het vermogen om spanningen te weerstaan. Daarom moet speciale aandacht worden besteed aan restspanningen, omdat in een omgeving die chloride-ionen bevat, restspanningen spanningscorrosiescheuren veroorzaken. De methode om restspanningen te verwijderen is spanningsarmgloeien.
Putcorrosie is de meest angstaanjagende vorm van corrosie. Er wordt gezegd dat dit de meest angstaanjagende corrosie is, en het is het meest passend om een gezegde uit de oudheid te gebruiken om dit probleem te beschrijven: “Een dijk van duizend mijl stort in in een mierennest.”
Er zijn twee belangrijke redenen waarom putcorrosie optreedt:
Ten eerste: als de materiaalsamenstelling ongelijkmatig is, zoals sensibilisatie, is austenitisch roestvast staal bijzonder gevoelig voor putcorrosie;
Ten tweede is de concentratie van corrosieve media in de omgeving ongelijkmatig, wat ook de oorzaak is van putcorrosie.
Zodra er putcorrosie optreedt, zal de lokale passivatiefilmlaag worden vernietigd en zal er concurrentie ontstaan tussen de actieve en de passivatietoestand. Zodra passivatie niet meer kan optreden, zal putcorrosie voortduren totdat het onderdeel is geperforeerd.
Austenitisch roestvast staal heeft geen vaste fase-transformatiepunt bij kamertemperatuur naar hoge temperatuur. Het belangrijkste doel van warmtebehandeling is het oplossen van de tijdens de verwerking gegenereerde carbiden in de matrix, waardoor de verdeling van de legeringselementen uniformer wordt.
Het austenitisch roestvast staal verwarmen tot een hoge temperatuur om de carbiden in de matrix op te lossen, en het vervolgens snel afkoelen tot kamertemperatuur. Tijdens dit proces zal het austenitische roestvast staal niet uitharden omdat er geen fasetransformatie plaatsvindt en de austenitische toestand op kamertemperatuur blijft. Dit proces wordt behandeling met vaste oplossingen genoemd.
Bij de behandeling met vaste oplossingen is het doel van snelle koeling alleen om de verdeling van koolstofatomen en legeringselementen uniformer te maken.
Als tijdens de behandeling met vaste oplossing van austenitisch roestvast staal de afkoelsnelheid te laag is, neemt de oplosbaarheid van koolstofatomen in de matrix af als de temperatuur daalt, en zullen carbiden neerslaan. Bovendien zijn koolstofatomen bijzonder gemakkelijk te combineren met chroom om M23C6-carbiden te vormen, die verdeeld zijn over de korrelgrenzen. Chroomuitputting treedt op in de korrelgrenzen en er treedt sensibilisatie op.
Nadat sensibilisatie optreedt in Austenitisch roestvrij staal, het moet boven 850ºC worden verwarmd. De carbiden zullen oplossen in een vaste oplossing, en vervolgens kan snelle afkoeling het sensibiliseringsprobleem oplossen.