Аустенитная нержавеющая сталь, как следует из названия, имеет аустенитную структуру. Термическая обработка аустенитной нержавеющей стали. очень важно, поскольку важной задачей аустенитной нержавеющей стали является устойчивость к коррозии. Если термическая обработка неправильная, его коррозионная стойкость будет значительно снижена. Эта статья в основном расскажет вам об этом. Термическая обработка аустенитных нержавеющих сталей.
Аустенитная нержавеющая сталь – это обычная нержавеющая сталь (сталь 18-8). Например, многие столовые приборы на кухне изготовлены из аустенитной нержавеющей стали. Аустенитная нержавеющая сталь, как следует из названия, имеет аустенитную структуру. Он немагнитен и не обладает прокаливаемостью.
Аустенитная нержавеющая сталь обладает очень высокой коррозионной стойкостью в окислительных средах. Под так называемой окислительной средой можно понимать просто среду, содержащую больше кислорода. Аустенитная нержавеющая сталь обладает хорошей прочностью, легко обрабатывается и формуется, поэтому имеет широкий спектр применения.
Аустенитная нержавеющая сталь в основном используется для обеспечения коррозионной стойкости, и на нее большое влияние оказывает термическая обработка. Коррозионная стойкость и кислотостойкость аустенитной нержавеющей стали в основном зависят от пассивации поверхности. Если пассивацию поверхности невозможно сохранить, она подвергнется коррозии.
Следовательно, аустенитная нержавеющая сталь не является полностью нержавеющим, он пригоден только для окислительных и кислых сред. Он не обладает сильной устойчивостью к специальным ионам. Термическая обработка аустенитной нержавеющей стали в основном влияет на пассивационную способность поверхностного слоя, тем самым влияя на ее коррозионные характеристики.
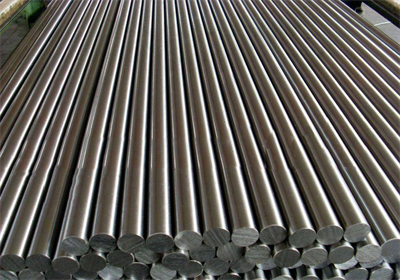
Поляризационная кривая нержавеющей стали 304, появляется зона пассивации анода
Равномерная коррозия является наиболее распространенным явлением коррозии, и равномерная коррозия зависит от равномерного распределения элементов хрома. Термическая обработка влияет на распределение элементов хрома, что, естественно, влияет на равномерную коррозионную стойкость аустенитной нержавеющей стали.
Межкристаллитная коррозия также является одним из важных коррозионных свойств для оценки аустенитной нержавеющей стали. Вообще говоря, если аустенитная нержавеющая сталь сенсибилизирована и на границах зерен выделяется большое количество шарикообразных карбидов, ее характеристики межкристаллитной коррозии будут значительно снижены.
Если аустенитная нержавеющая сталь сенсибилизирована, сильная межкристаллитная коррозия произойдет даже в самой обычной электрохимической среде.
Коррозионное растрескивание под напряжением является наиболее распространенным видом разрушения аустенитной нержавеющей стали. Всем следует отметить, что коррозионное растрескивание под напряжением зависит от двух основных факторов:
Во-первых, должно существовать напряжение, которое может быть приложенным напряжением или остаточным напряжением;
Во-вторых, наиболее распространены ионы, чувствительные к коррозионному растрескиванию под напряжением, такие как ионы галогена, особенно ионы хлорида.
При использовании аустенитной нержавеющей стали ее способность выдерживать напряжения часто не используется, поэтому особое внимание следует уделять остаточному напряжению, поскольку в среде, содержащей ионы хлорида, остаточное напряжение вызывает коррозионное растрескивание под напряжением. Методом снятия остаточных напряжений является отжиг для снятия напряжений.
Питтинговая коррозия – самая опасная форма коррозии. Говорят, что это самая страшная коррозия, и для описания этой проблемы лучше всего использовать поговорку древних: «Дамб длиной в тысячу миль обрушивается в муравейнике».
Существует две основные причины возникновения питтинговой коррозии:
Во-первых, если состав материала неравномерен, например, из-за сенсибилизации, аустенитная нержавеющая сталь особенно склонна к точечной коррозии;
Во-вторых, концентрация агрессивных сред окружающей среды неравномерна, что также является причиной питтинговой коррозии.
При возникновении питтинговой коррозии локальный слой пассивационной пленки разрушается, и возникает конкуренция между активным и пассивационным состояниями. Если пассивация не может произойти, питтинговая коррозия будет продолжаться до тех пор, пока компонент не будет перфорирован.
Аустенитная нержавеющая сталь не имеет точки перехода твердой фазы при температуре от комнатной до высокой температуры. Основная цель термообработки – растворить в матрице карбиды, образующиеся при обработке, тем самым сделать распределение элементов сплава более равномерным.
Нагрев аустенитной нержавеющей стали до высокой температуры для растворения карбидов в матрице, а затем быстрое ее охлаждение до комнатной температуры. Во время этого процесса аустенитная нержавеющая сталь не затвердевает, поскольку не происходит фазового превращения, и аустенитное состояние сохраняется при комнатной температуре. Этот процесс называется обработкой твердого раствора.
При обработке твердым раствором цель быстрого охлаждения состоит только в том, чтобы сделать распределение атомов углерода и легирующих элементов более равномерным.
Если во время обработки аустенитной нержавеющей стали твердым раствором скорость охлаждения слишком медленная, то при понижении температуры растворимость атомов углерода в матрице снижается, и карбиды выпадают в осадок. Более того, атомы углерода особенно легко соединяются с хромом с образованием карбидов M23C6, которые распределяются по границам зерен. В границах зерен происходит обеднение хромом и происходит сенсибилизация.
После возникновения сенсибилизации аустенитная нержавеющая сталь, его следует нагреть выше 850°C. Карбиды растворятся в твердый раствор, а затем быстрое охлаждение может решить проблему сенсибилизации.