Östenitik paslanmaz çelik, adından da anlaşılacağı üzere östenit yapıya sahiptir. Östenitik paslanmaz çeliğin ısıl işlemi çok önemlidir çünkü östenitik paslanmaz çeliğin önemli görevi korozyon direncidir. Isıl işlem uygun değilse korozyon direnci büyük ölçüde azalacaktır. Bu makale esas olarak size bundan bahsediyor. Östenitik paslanmaz çeliklerin ısıl işlemi.
Östenitik paslanmaz çelik yaygın bir paslanmaz çeliktir (18-8 çelik). Örneğin mutfaktaki birçok sofra takımı östenitik paslanmaz çelikten yapılmıştır. Östenitik paslanmaz çelik, adından da anlaşılacağı üzere östenit yapıya sahiptir. Manyetik değildir ve sertleşebilme özelliği yoktur.
Östenitik paslanmaz çelik, oksitleyici ortamlarda çok güçlü korozyon direncine sahiptir. Oksitleyici ortam olarak adlandırılan ortam, daha fazla oksijen içeren bir ortam olarak basitçe anlaşılabilir. Östenitik paslanmaz çelik iyi bir tokluğa sahiptir ve işlenmesi ve şekillendirilmesi kolaydır, bu nedenle geniş bir kullanım alanına sahiptir.
Östenitik paslanmaz çelik esas olarak korozyon direnci amacıyla kullanılır ve ısıl işlemin bunda büyük etkisi vardır. Östenitik paslanmaz çeliğin korozyon direnci ve asit direnci esas olarak yüzey pasivasyonuna bağlıdır. Yüzey pasivasyonu sürdürülemezse korozyona uğrar.
Bu nedenle, Östenitik paslanmaz çelik tamamen paslanmaz değildir, sadece oksitleyici ortamlar ve asidik ortamlar için uygundur. Özel iyonlara karşı güçlü bir dirence sahip değildir. Östenitik paslanmaz çeliğin ısıl işlemi esas olarak yüzey katmanının pasivasyon yeteneğini etkiler, dolayısıyla korozyon performansını etkiler.
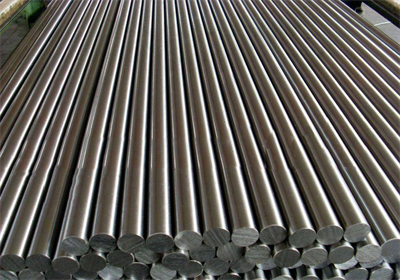
304 paslanmaz çelik polarizasyon eğrisi, anot pasivasyon bölgesi görünür
Düzgün korozyon en yaygın korozyon olgusudur ve düzgün korozyon, krom elementlerinin düzgün dağılımına bağlıdır. Isıl işlem, östenitik paslanmaz çeliğin tekdüze korozyon direncini doğal olarak etkileyen krom elementlerinin dağılımını etkiler.
Taneler arası korozyon aynı zamanda östenitik paslanmaz çeliğin değerlendirilmesinde önemli korozyon özelliklerinden biridir. Genel olarak konuşursak, östenitik paslanmaz çelik hassaslaştırılırsa ve çok sayıda boncuk benzeri karbür tanecik sınırlarında çökelirse, tanecikler arası korozyon performansı büyük ölçüde azalacaktır.
Östenitik paslanmaz çelik hassaslaştırılırsa, çok sıradan bir elektrokimyasal ortamda bile şiddetli taneler arası korozyon meydana gelecektir.
Gerilim korozyonu çatlaması, östenitik paslanmaz çeliğin en yaygın arıza modudur. Stresli korozyon çatlağının iki ana faktöre bağlı olduğunu herkesin bilmesi gerekir:
İlk olarak, stres veya artık stres uygulanabilecek bir stres olmalıdır;
İkincisi, halojen iyonları, özellikle de klorür iyonları gibi gerilim korozyonu çatlamasına duyarlı iyonlar en yaygın olanlardır.
Östenitik paslanmaz çelik kullanıldığında, strese dayanma yeteneği sıklıkla kullanılmaz, dolayısıyla artık gerilime özel dikkat gösterilmelidir çünkü klorür iyonları içeren bir ortamda artık gerilim, gerilimli korozyon çatlamasına neden olur. Artık gerilimi gidermenin yöntemi gerilim giderme tavlamasıdır.
Çukur korozyonu, korozyonun en korkunç şeklidir. En korkunç korozyon olduğu söylenir ve bu sorunu anlatmak için eskilerin bir deyişini kullanmak en doğrusudur: "Binlerce kilometrelik bir hendek bir karınca yuvasına çöker."
Çukur korozyonunun oluşmasının iki ana nedeni vardır:
İlk olarak, eğer malzeme bileşimi hassaslaşma gibi dengesizse, ostenitik paslanmaz çelik özellikle oyuklanma korozyonuna eğilimlidir;
İkincisi, çevresel aşındırıcı ortamın konsantrasyonu eşit değildir ve bu aynı zamanda oyuklanma korozyonunun da nedenidir.
Çukurlaşma korozyonu oluştuğunda, yerel pasivasyon film tabakası yok edilecek ve aktif ve pasifizasyon durumları arasında rekabet oluşacaktır. Pasifleştirme gerçekleşemediğinde, bileşen delininceye kadar çukurlaşma korozyonu devam edecektir.
Östenitik paslanmaz çeliğin oda sıcaklığından yüksek sıcaklığa kadar katı faz dönüşüm noktası yoktur. Isıl işlemin temel amacı, işleme sırasında oluşan karbürleri matris içinde çözerek alaşım elementlerinin dağılımını daha düzgün hale getirmektir.
Karbürlerin matris içinde çözünmesi için östenitik paslanmaz çeliğin yüksek bir sıcaklığa ısıtılması ve ardından hızlı bir şekilde oda sıcaklığına soğutulması. Bu işlem sırasında östenitik paslanmaz çelik, faz dönüşümü olmadığından ve östenitik durum oda sıcaklığında kalacağından sertleşmeyecektir. Bu işleme katı çözelti muamelesi denir.
Katı çözelti arıtımında hızlı soğutmanın amacı yalnızca karbon atomlarının ve alaşım elementlerinin dağılımını daha düzgün hale getirmektir.
Östenitik paslanmaz çeliğin katı çözelti işlemi sırasında soğutma hızı çok yavaşsa sıcaklık düştükçe matristeki karbon atomlarının çözünürlüğü azalır ve karbürler çöker. Üstelik karbon atomlarının kromla birleşerek tane sınırlarında dağılmış M23C6 karbürleri oluşturması özellikle kolaydır. Tane sınırlarında krom tükenmesi meydana gelir ve hassasiyet meydana gelir.
Hassasiyet oluştuktan sonra Östenitik paslanmaz çelik850°C'nin üzerinde ısıtılmalıdır. Karbürler katı bir çözelti halinde çözülecek ve ardından hızlı soğutma, hassasiyet sorununu çözebilir.