TC4 titanium alloy is an α-β type titanium alloy successfully developed by the United States in 1954, containing 6% α stable element and 4% β stable element V. The nominal composition of it is 7.0 aluminum equivalent, molybdenum equivalent 2.9, and contains 10%-15% beta phase in the annealed state. Al improves the room temperature strength and thermal strength properties of alloys by solid solution strengthening α phase in the Ti-Al-V system, while V is one of the few alloying elements that can improve both strength and plasticity in titanium alloys. The beneficial effect of V on the plasticity of titanium alloys is that it does not increase the c/a-axis ratio of the α-state lattice-like most alloying elements, but reduces the ratio, thereby increasing the formation of α-phase and avoiding long-term use. Alloy embrittlement occurs during the process.
The main features of TC4 titanium alloy are excellent comprehensive performance and good process performance. It has moderate room temperature strength and high-temperature strength, good creep resistance and thermal stability, high fatigue resistance and crack propagation resistance in seawater, and satisfactory fracture toughness and thermal salt stress corrosion resistance, The sensitivity to hydrogen is also smaller than that of TC2 and TC1 alloys. It is suitable for the manufacture of various parts that work in a wide temperature range of -196~450 °C, especially the parts designed with the principle of damage tolerance limit. TC4 also has excellent process plasticity and superplasticity, suitable for forming with various pressure processing methods, and welding and machining in various ways.
The main semi-finished forms of TC4 titanium alloy are bars, forgings, sheets, thick plates, profiles, wires, etc., and are also used for castings (ZTC4).
TC4ELI Titanium Alloy
TC4ELI is an improved version of TC4, the main difference is the different Al content and lower content of interstitial elements Fe, N, H, and O.
TC4ELI titanium alloy has become a medical-surgical implant due to its good biocompatibility, low elastic modulus, low density, good corrosion resistance, non-toxicity, high yield strength, long fatigue life, and large plasticity at room temperature, and easy forming. ideal material. Medical TC4ELI titanium alloy sheet is mainly used for skull repair, bone setting, etc., which has higher requirements on its strength, fatigue life, and plasticity.
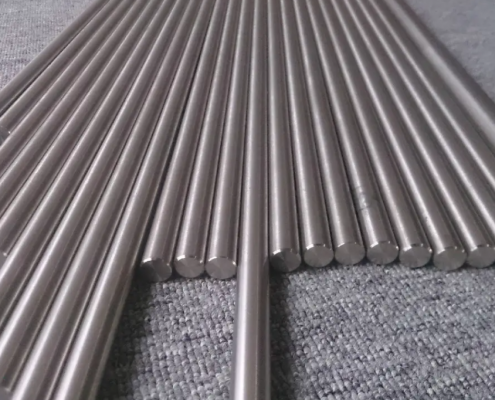
Titanium alloy is an alloy composed of titanium elements and other elements. Titanium has two kinds of isomorphic crystals: titanium is an allotrope with a melting point of 1668 °C, and it is a close-packed hexagonal lattice structure below 882 °C, called α-titanium; above 882 °C, it is body-centered cubic. A lattice structure is called beta-titanium. Using the different characteristics of the above two structures of titanium, appropriate alloying elements are added to gradually change the phase transition temperature and component content to obtain titanium alloys with different structures.
On the basis of TC4 alloy, TC4 ELI titanium alloy reduces the content of interstitial elements C, O, N and impurity element Fe, and the strength is reduced, but the capacity and toughness can be significantly improved. TC4 ELI has good plasticity, toughness, good welding performance, and low-temperature performance, and is widely used in important fields such as low-temperature engineering, medical treatment, ships, and aircraft.
TC4 alloy can be used in an ordinary environment or high-temperature environment, and TC4 ELI alloy can be used in an ultra-low temperature environment
Similar grades of TC4 titanium alloy and TC4ELI titanium alloy are T-6A-4V/Grade 5 (American grade), BT 6 (Russian grade), IMI 318 (British grade), TiAI6V4 (German grade).
Medical equipment manufacturing In the human body, the bone and joint damage caused by trauma and tumor, artificial joints, bone plates, and screws are made of titanium and titanium alloys, which are now widely used in clinical practice. Also used in hip joints (including femoral heads), knee joints, elbow joints, metacarpophalangeal joints, interphalangeal joints, mandibles, artificial vertebral bodies (spinal orthoses), pacemaker housings, artificial hearts (heart valves), artificial dental implants, titanium-nickel dental orthodontics and titanium mesh in cranioplasty, etc.
Titanium and titanium alloys are receiving increasing attention due to their high specific strength, good biocompatibility, and good resistance to body fluid corrosion.
Ti 6Al-4V ELI is a grade of Ti 6Al-4V with a smaller structure gap, which can achieve maximum toughness and is suitable for seawater and low-temperature environments. This grade of alloy is usually used in the annealed condition. Ti 6Al-4V is a good choice for medical implants.
The production process is: relaxation annealing and air cooling at 900-120 degrees Fahrenheit for 1-4 hours. Double annealed, round bars and forgings are solution annealed at a beta transition temperature of 50-100 degrees Fahrenheit, held for at least 1 hour and then air-cooled, then reheated at 1300-1400 degrees Fahrenheit for at least 1 hour, air-cooled. Relaxation annealing is suitable after welding